Ross Grassick
Warehouse Management
How to Improve the Efficiency and Productivity of Your Warehouse
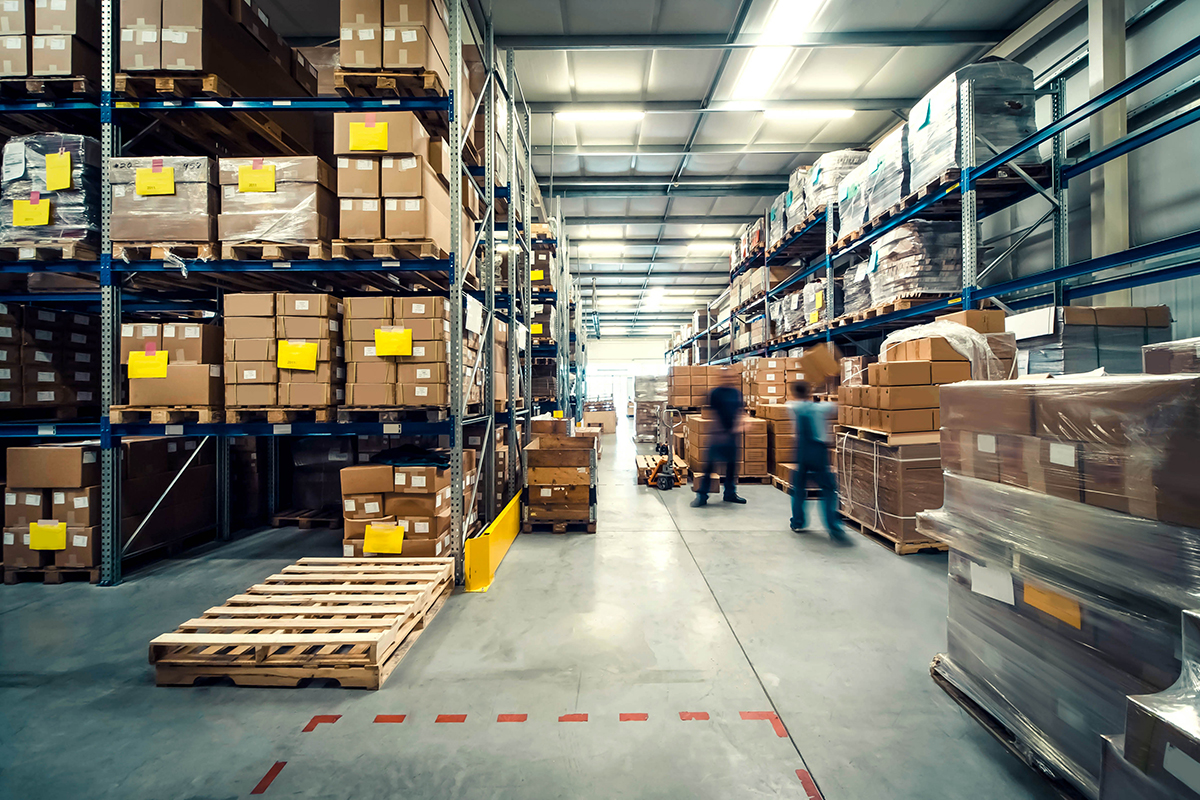
Having an efficient warehouse is crucial to business success, and is the key to a productive logistics operation. In this guide, we’ll show you some key areas that must be looked at to achieve the levels of productivity and safety needed in today’s high-speed storage and distribution facilities.
Take stock of warehouse equipment
The first thing you need to know is what equipment you’ll be using and where it will be used in your warehouse space. Having an understanding of the layout of your warehouse and its access areas will play a key role in boosting productivity.
Ask yourself questions. Is all the equipment suitable to work in aisles, or do you need to zone units into areas? (As not doing so might slow operations down and in some cases bottleneck goods handling). Also don’t use existing equipment in a new layout if it doesn’t suit the racking design. While equipment is expensive, the inefficiency caused by mismatched equipment can diminish productivity and cause damage to racks or stock.
Assess warehouse floor & entry points
The warehouse floor is another factor you need to consider, as the type of floor you have will determine the types of machines you can work with. If you have a rough floor, then you’re limited to machines with larger tyres that will wear quickly with use. This also will slow operations down and has the possibility of causing stock and equipment damage.
If you have any slopes and ramps then you need to be mindful that the break over angle of your machine can cause it to get stuck or scrape when going over, resulting in damage to your machine. Ramps, in general, tend to slow operations down and, if possible, shouldn’t be a part of normal stock flow.
Inspect the layout of your lighting fixtures
From the bottom of the warehouse to the top, you need to consider your lighting, as poor lighting increases the chance of accidents and stock damage. If your warehouse already has skylights, then you’ll get all the natural sunlight that comes through at no extra cost. If you don’t have skylights, it’s worth considering state of the art LED lighting is low cost and provides clean light.
Before installing lights, you need to consider the positioning of the lighting features and how it will affect the warehouse workflow. As a general rule, its best to install lighting over the aisles, since that’s where machines are operating most of the time. However, you may not be able to install lights where sensors are in use or if they are obstructing racks.
Manage your warehouse traffic
Traffic management can be overlooked, but it’s also something you need to consider when attempting to maximise your warehouse productivity. Drive through racking is a good idea as it can provide shorter routes for your equipment, cutting down on time. Having a plan and educating your employees on operation flows will allow everyone to exercise efficient movement of goods and reduce the likelihoods of accidents, ensuring the safety of everyone involved as well as improving operations.
Have a maintenance plan in place
Downtime in equipment use due to breakdowns means lost productivity and money down the drain. Considering this, you need a maintenance plan in place to ensure that all equipment has regular servicing done to prevent future breakdowns. Make sure that operators carry out pre-start checks, as prevention is better than repair from failure. You’ll also be keeping your workplace safe and productive by having working machines.
Train your warehouse employees
Employee training is imperative in running an efficient warehouse. The employees operating the equipment will know where they can operate to be most productive. If there are changes to the warehouse floor plan, then employees will have to be educated on what’s expected and who should give way. Refresher training is also important, especially when equipment is changed or upgraded.
Upgrade your technology
You may also want to consider upgrading or changing your equipment. With the rise of battery electric forklifts, performance is now faster, making materials handling more efficient. Battery electric forklifts cost less to run, especially when you compare them to fuel forklifts with the running costs over time. The electric option will not only be less expensive on fuel, but it will improve the warehouse working environment by reducing noise and exhaust pollution, as well as heat and dust. This makes your warehouse a safe and happy place to work, as well as keeping the stock cleaner.
With the rise of technology, we’re able to speed up work and get tasks done more efficiently. Cameras are a great piece of technology that can be attached to your forklifts so operators can have a better view of their operation. There are wireless cameras available that can be attached to forklift carriages, so operators can also see down the line, making visibility more accurate and reliable. You can fit these cameras aftermarket to your existing warehouse equipment. They may seem costly initially, but they will save in the damage of stock, as well as increase productivity.
Run your warehouse ahead of the game
Never say “if it’s not broken, don’t fix it”. There are always ways to improve productivity and safety in your logistics operation. Lencrow Forklifts has been in operation for more than 40 years and our experienced staff are happy to discuss any of the points discussed in this article.